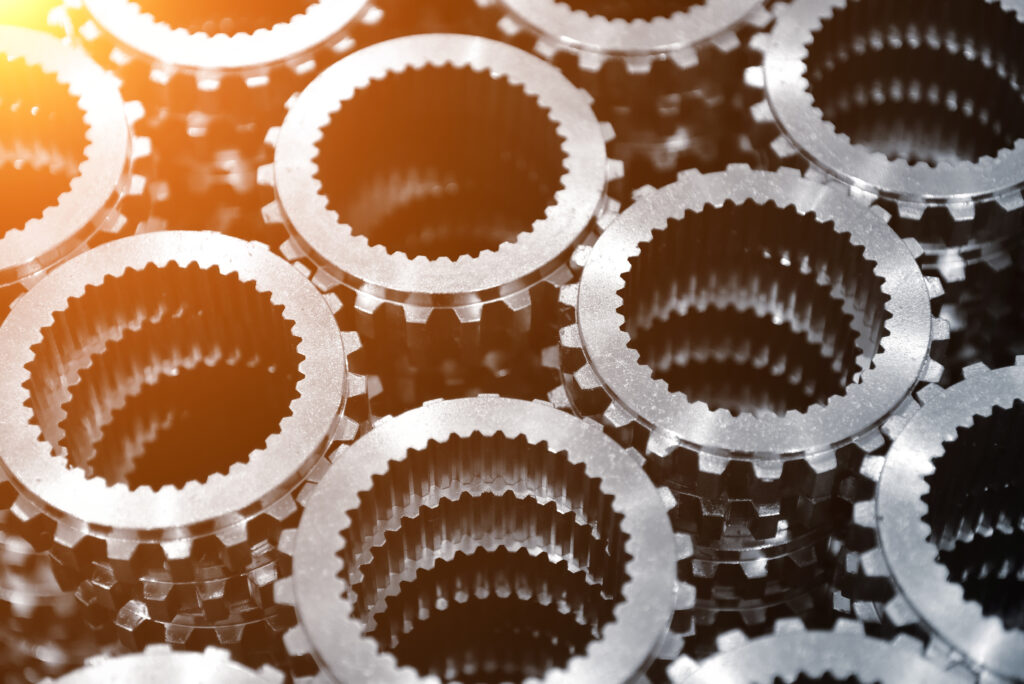
Planetary gear motors and worm gears are key components in a wide range of industrial applications, from robotics to automation, from power transmission to machine tools. Their ability to transmit power efficiently and precisely depends not only on mechanical design, but also on the choice of materials used for the gears and transmission components.
The selection of gear material depends on various factors, including the type of application, operating temperature, load and rotational speed. In high-speed applications, such as precision gears for robotics, materials offering fatigue resistance and low friction are preferred. In heavier applications, such as industrial motors, materials that are more resistant to corrosion and wear, such as special steel alloys, are used.
1. The main materials used for planetary gears
Planetary gearmotors, due to their compact design and ability to distribute loads over several gears, are often chosen for applications requiring high performance in small spaces.
The choice of materials for these gears is crucial to ensure mechanical strength, hardness and the ability to withstand high loads without suffering deformation or premature failure.
Alloy steels
Alloy steels are among the most commonly used materials for planetary gears. due to their tensile strength and ability to withstand heavy loads. The most common steels include:
Carbon steels: these steels are easy to machine and can be heat-treated to improve their mechanical properties. Once hardened, carbon steel gears offer good fatigue resistance.
Carbon steels. Carbon steels are ideal for high-strength applications. However, in some cases, aluminium alloys are used to reduce weight without compromising strength too much, such as in applications requiring energy efficiency and light engines.’
Alloy steels (such as nickel or chromium steels): These steels are used in applications where higher fatigue and corrosion resistance is required. The alloy content improves the wear resistance and hardness of the material.
Heat-treated steels
To further improve the durability and wear resistance of gears, heat treatments such as carburisation or surface hardening are often used. Carburisation, in particular, results in a softer and more ductile core, while the surface becomes much harder, making the gears wear-resistant without compromising their toughness.
Aluminium alloys
In some applications, the gears must be particularly light without compromising strength too much. Aluminium alloys are used to reduce the overall weight of the gearmotor while still maintaining good strength. Although not common in ultra-high load applications, aluminium alloys are ideal for applications where energy efficiency is crucial.
2. Advanced materials for worm gears.
Worm screws are particularly useful when a high reduction ratio is required in tight spaces. Their design allows the speed of rotation to be reduced and torque to be increased efficiently. However, worm screws are subject to high levels of friction, which makes the choice of materials even more critical.
Alloy steels and surface treatments
As with planetary gears, alloy steels are also used for worm gears. However, for worm gears, wear resistance and the ability to work with high friction are particularly important. Surface treatments such as chrome plating or nitriding are used to improve corrosion resistance and increase surface hardness, reducing wear caused by contact between the screw and the gear.
Bronze alloys for gears
A key feature of worm screws is that the gear that interacts with the screw is often made of bronze or bronze alloys. Bronze has excellent wear-resistant properties, as well as good natural lubrication capacity, reducing friction between the screw and the gear.
Composite materials In some applications, especially in the area of low speed and torque transmissions, composite materials such as glass-fibre reinforced polymers can be used for worm gears. These materials are lightweight and significantly reduce energy consumption, but are still relatively expensive compared to metals.
3. The impact of surface treatments on materials
Surface treatments are essential to improve material properties and to ensure that gears and worm gears possess the necessary hardness to withstand loads and stresses during operation. Some of the most common treatments include:
Carbonitriding
Carbonitriding is a thermochemical process used to improve the surface properties of gears, in particular to increase their wear resistance, hardness and fatigue strength. It is particularly useful in gearmotor gears, which must withstand high loads and operate in harsh working environments.
The carbonitriding process involves the simultaneous introduction of carbon and nitrogen into the steel surface. The combination of these two elements results in a material with a high surface hardness while maintaining good toughness in the core of the component, which is crucial for the fatigue strength of gears.
Benefits of carbonitriding on gearmotor gears:
- Increased surface hardness: The surface hardness of the gears increases significantly, improving wear and fatigue resistance.
- Fatigue resistance: The combination of carbon and nitrogen creates a surface structure that better withstands the loading and unloading cycles typical in geared motors.
- Migliore prestazione a lungo termine: Gli ingranaggi trattati tramite carbonitrurazione sono in grado di sopportare carichi pesanti e lavorare per periodi più lunghi, riducendo il rischio di usura e rottura.
Chrome plating and PVD (Physical Vapor Deposition) coatings
Chrome plating and PVD coatings are used to improve corrosion and wear resistance, especially in aggressive environments or applications with high operating temperatures. These coatings create a protective layer that not only improves tribological properties, but also increases the surface hardness of gears.
4. Composite materials and ceramics: the new frontier
In recent years, the industry has seen the introduction of advanced composite materials and ceramic materials for applications where traditional metals are no longer sufficient for optimal performance. Unfortunately, these materials are not yet widely used in gearmotors due to high costs and difficulties in processing, but they represent a possible direction for the future.
Carbon-fibre reinforced polymers
Composite materials, such as carbon-fibre reinforced polymers, can be used to reduce the weight of gears while maintaining good mechanical strength and a low coefficient of friction. These materials are particularly useful in high-speed applications where energy consumption must be minimised.
High-performance ceramics
Ceramics (e.g. silicon carbide or aluminium oxide) can be used in high temperature or high pressure environments. They are extremely durable materials, but require very precise production techniques. The use of ceramics may, in the future, become more common in precision geared motors and worm screws for high-performance applications.
5. The choice of material according to application
The selection of the ideal material depends heavily on the type of application and operating conditions. For example:
- High speed and low torque: In applications such as motors for robotics and precision systems, lightweight, low-friction materials such as aluminium alloys or reinforced polymers are preferred.
- High loads and low speeds: In heavy industrial applications, such as machine tools or power reducers, heat-treated alloy steels are the preferred choice for strength and durability.
- Extreme temperature conditions: In applications operating at high temperatures (e.g. in the aerospace or renewable energy sectors), ceramic materials or alloys resistant to corrosion and heat can be the ideal solution.
In conclusion, the choice of material for gears in planetary gearmotors and worm gears is crucial to ensure maximum efficiency, durability and resistance to operational stresses. Advances in materials, from heat-treated metals to advanced polymers, offer new opportunities to optimise performance and reduce operating costs. As materials technology evolves, the industry will be able to meet future challenges with increasingly efficient and sustainable solutions.